4 Factors Affecting the Boiling Heat Transfer of Refrigerant Liquid
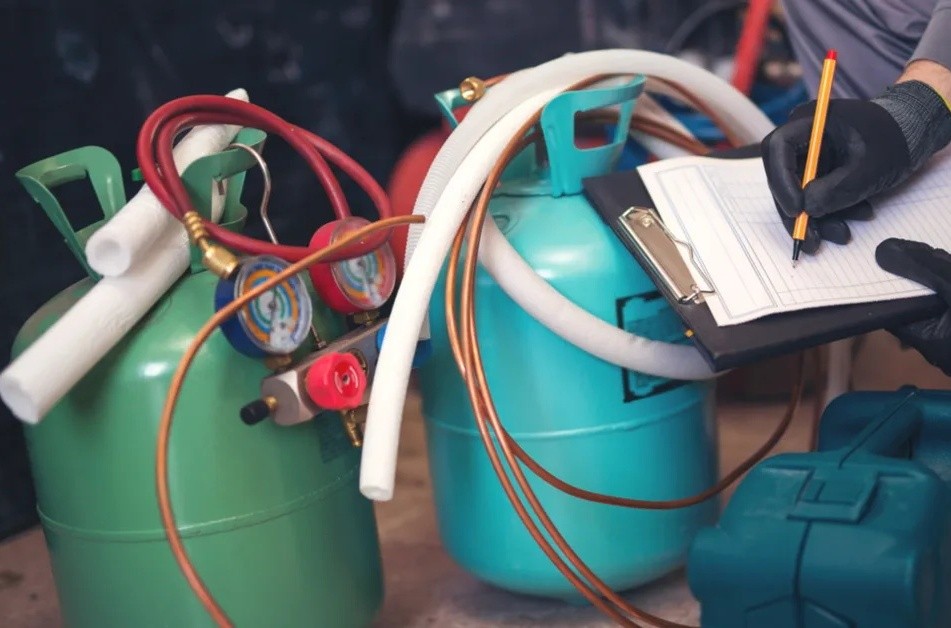
In the evaporator, the heat of the cooling medium is transferred to the refrigerant through the heat transfer wall, so that the liquid refrigerant absorbs heat and vaporizes. The change in the state of the refrigerant in the evaporator is actually a boiling process, which is customarily called evaporation. Here are mainly four factors that affect the boiling heat transfer of refrigerant liquid.
1. Influence of refrigerant liquid physical properties
Relevant physical properties such as the thermal conductivity, density, viscosity, and surface tension of the refrigerant liquid have a direct effect on the boiling heat transfer coefficient.
A refrigerant with a larger thermal conductivity has a smaller thermal resistance in the heat transfer direction and a larger boiling heat transfer coefficient.
Under normal working conditions of the evaporator, the temperature difference between the refrigerant in the evaporator and the heat transfer wall is generally only 2~5℃.
The intensity of the convective heat transfer depends on the convective movement of the refrigerant liquid during the vaporization process. During the boiling process, the movement of bubbles in the liquid causes the liquid to be disturbed, which increases the possibility of contact between various parts of the liquid and the heat transfer wall, making it easier for the liquid to absorb heat from the heat transfer wall and the boiling process is faster.
The refrigerant liquid with lower density and viscosity will be stronger by this disturbance, and its convective heat transfer coefficient will be larger.
The greater the density and surface tension of the refrigerant liquid, the larger the diameter of the bubbles during the vaporization process, the longer the time for bubbles to leave the heat transfer wall, the fewer bubbles are produced per unit time, and the smaller the heat transfer coefficient.
Generally speaking, the thermal conductivity of Freon is smaller than that of ammonia, and its density, viscosity, and surface tension are larger than that of ammonia, so its boiling heat transfer coefficient is smaller than that of ammonia.
2. Influence of refrigerant liquid wetting ability
If the refrigerant liquid has a strong wetting ability on the heat transfer surface, the bubbles generated during the boiling process have fine roots, which can be quickly separated from the heat transfer surface, and the heat transfer coefficient will be larger.
On the contrary, if the refrigerant liquid cannot wet the heat transfer surface well, the roots of the bubbles formed will be very large, reducing the number of vaporization cores, and even forming a gas film along the heat transfer surface, which significantly reduces the heat transfer coefficient.
Several commonly used refrigerants are all wetting liquids, but the wetting ability of ammonia is much stronger than that of Freon.
3. The influence of refrigerant boiling temperature
During the boiling of the refrigerant liquid, the more bubbles generated per unit time on the heat transfer wall of the evaporator, the greater the boiling heat transfer coefficient.
The number of bubbles generated in a unit time is related to the length of time the bubbles are generated to leave the heat transfer wall. The shorter the time, the more bubbles are generated in the unit time. In addition, if the diameter of the bubble when it leaves the wall surface is smaller, the time from generation to the departure of the bubble will be shorter.
When the bubble leaves the wall, its diameter is determined by the balance of the buoyancy of the bubble and the surface tension of the liquid. Buoyancy forces the bubbles to leave the wall, while the surface tension of the liquid prevents the bubbles from leaving. The buoyancy of the bubble and the surface tension of the liquid is also affected by the density difference (the density difference between liquid and vapor) at the saturation temperature. The buoyancy of the bubble is proportional to the density difference. The surface tension of the liquid is proportional to the fourth power of the density difference.
Therefore, as the density difference increases, the rate of increase of the liquid surface tension is much larger than the rate of increase of the bubble buoyancy. At this time, the bubble can only rely on volume expansion to maintain balance, so the diameter of the bubble when it leaves the wall is Big.
The size of the density difference is related to the boiling temperature. The higher the boiling temperature, the smaller the density difference at the saturation temperature, the faster the vaporization process, and the greater the heat transfer coefficient.
It is explained above that when the same refrigerant is used in the same evaporator, the heat transfer coefficient increases with the increase of the boiling temperature.
4. Influence of evaporator structure
During the liquid boiling process, bubbles can only be generated on the heat transfer surface, and the effective heat transfer surface of the evaporator is the part in contact with the refrigerant liquid. Therefore, the size of the boiling heat transfer coefficient is related to the structure of the evaporator.
The experimental results show that the boiling heat transfer coefficient of the finned tube is greater than that of the smooth tube, and that of the tube bundle is greater than that of a single tube. This is because after adding fins, under the same conditions of saturation temperature and heat load per unit area, the conditions of bubble generation and growth, finned tubes are more advantageous than smooth tubes.
As the number of vaporized cores increases and the bubble growth rate decreases, the bubbles are easily separated from the heat transfer wall. The experimental results also show that the boiling heat transfer coefficient of the finned tube bundle is greater than that of the smooth tube bundle.
According to some information, at the same saturation temperature, the boiling heat transfer coefficient of Rl2 in the finned tube bundle is 70% larger than that of the smooth tube bundle, and R22 is 90% larger.
According to the above analysis, the structure of the evaporator should ensure that the refrigerant vapor can quickly leave the heat transfer surface. In order to effectively use the heat transfer surface, the vapor generated after the liquid refrigerant is throttled should be separated from the liquid before entering the evaporator, and in the operation management, the evaporator should maintain a reasonable refrigerant liquid flow rate.
In addition, the oil contained in the refrigerant also has a certain influence on the boiling heat transfer coefficient, and its degree of influence is related to the oil concentration. Generally speaking, when the refrigerant oil content is not more than 6%, this effect can be ignored. When the oil content is larger, the boiling heat transfer coefficient will be reduced.
We can change the effect of refrigerant liquid boiling heat exchange by reasonably controlling some of the above factors so that the refrigeration system can exert more refrigeration effects. If you want to know more about refrigerants after reading the above, you can get a comprehensive solution by contacting us.
As a professional supplier of refrigerants and fluoropolymers, we have won praise and trust from many customers with our excellent R&D technology and high-quality products. We have a professional production team and have established a complete quality inspection system, which can fully control the quality of our products. At the same time, we will provide thoughtful one-stop service and effective solution technology according to the needs of customers. If you are interested in our refrigerants, please contact us immediately!